Predictive maintenance for wind turbines - an interview with Boldare’s machine learning engineers
One of the critical issues for the wind energy industry is the maintenance of wind farms, including component failures and replacement. The scale of this problem is significant. Maintenance operations can constitute approximately 20-25% of the total levelized cost per kWh, and each failure can cost up to $250,000 to resolve. Reactive maintenance is no longer a solution.

Table of contents
This is why the industry is on the search for an efficient and applicable solution which can help reduce energy loss, cut the cost of unexpected failures and, putting it simply, save money. This issue could be addressed by smart use of machine learning algorithms which, based on data from wind turbines, can help predict failure events up to 60 days before they occur.
How can machine learning help with predictive maintenance? What is necessary to build models which can predict turbine failures? What data is required to make it happen?
To find the answers to these questions, I spoke with Paweł Krynicki, Tomasz Bąk and Paweł Capaja - members of Boldare’s Machine Learning Team which is working on a machine learning solution for wind turbine predictive maintenance.
This interview is based on a webinar by Boldare: “Predictive Maintenance with Machine Learning Algorithms”. You can find the video from the webinar HERE or under the interview.
Guys, I would like to ask you how did it happen that you got interested in the topic of predictive maintenance?
Tomasz Bąk (Ph.D., machine learning engineer): Our team has general experience in various implementations of machine learning. However, we do not limit ourselves only to building software according to the customer’s expectations. We also look for business problems which can be solved using machine learning.
During such research, we came across the problem of predictive maintenance in the wind energy industry. It was just before the Wind Europe trade show, so we decided that it was the best moment to start.
Can you elaborate on this? What is the Wind Europe trade show?
Paweł Capaja ( Product Designer): Expo Wind Europe is the wind community connecting all the enterprises in the market and allowing them to share knowledge and influence the market’s direction. They claim to have over 450 members, and are active in over 40 countries. At the same time, it is the biggest event for the wind industry in Europe, happening in Hamburg this year. It includes the conference, trade show and hackathon “Hack the Wind”, in which our team took part.
What was the aim of Hack the Wind?
Paweł Capaja: “Hack the Wind” had two challenges, and we participated in the one connected with predictive maintenance (the second one was about building a blockchain solution). Our goal was to create an algorithm which could determine possible failures of selected components from wind turbines, 60 days ahead, with the possible highest accuracy. Moreover, the solution had to be presented in the form of a product.
What was your final score at Hack the Wind?
Paweł Krynicki (machine learning engineer): There were two stages of the competition. One was strictly technical - to evaluate the predictive model regarding its efficiency and accuracy. This stage also included a quick pitch of the solution we’ve built, but the focus was put rather on the numeric results and the description of the algorithms we used. In this case, our solution took the 2nd place.
To give you some background, we were predicting failures of 5 wind turbines from 1 offshore wind farm for the year 2017. The machine learning model has correctly predicted 11 malfunctions out of 12: 2 failures were related to the malfunctioning gearbox, 2 to the generator bearings, 1 to the transformer and 6 to the hydraulic system.
There was only one malfunction which our model didn’t anticipate, and that was related to the generator. In total, we would have saved over 192,490 Euros on the maintenance of the wind farm but due to a high rate of false positives - which cause costs related to calling out a maintenance team to inspect the turbine - our total generated savings were a bit lower, around 12.5K per turbine. On average, our model was correctly predicting failures of the components almost forty days before they actually occurred.
The 2nd stage was related to the product we have built upon the predictive algorithm. Our team created a working prototype of a software application supporting the entire maintenance process - from predicting the failure of certain components to ordering required parts, updating the inventory and ultimately fixing the malfunction. In this stage, we made it to the top 3.
Based on your research at the Wind Europe trade show and conference could you name the critical challenges for the wind industry?
Tomasz Bąk: Let me point out the three most significant issues:
- Reduce the cost and repair time. The majority of operational costs in the wind industry come from maintenance, and can therefore be reduced. This problem can be solved directly using predictive maintenance. However, predictive maintenance has also indirect advantages: longer lifespan for the turbines and the optimization of energy production.
- Different data formats in different systems. This is a more fundamental problem because without data standardization it is impossible to implement predictive maintenance.
- Problems with the grid. The optimization of energy transmission is needed (which can also be solved using machine learning) and the development of a more modern infrastructure.
In your opinion, what is the future of the wind industry? In what direction is it going?
Tomasz Bąk: As a machine learning engineer, I would answer: give me your data and then I can make the prediction {laugh}. But, ok, I will try to step into a futurologist’s shoes.
I have read about new types of wind turbine, like turbines in the shape of birds, or power-generating kites. So this is the future, the visible one. It will be interesting because we can observe this evolution with our eyes.
There will also be another, less visible future, which will be driven by artificial intelligence. The application of machine learning will be more comprehensive than it is now. I think that it won’t be limited to predictive maintenance. It would be useful for wind energy distribution or effective wind utilization. Maybe we will have self-repairing wind turbines?
I’m just guessing. However, I am quite sure that in the future machine learning will play a significant role.
Let’s focus now on the topic of predictive maintenance. What are the characteristics of a good predictive maintenance solution for wind turbines?
Paweł Krynicki: Based on our research on the market, we noticed that the majority of the solutions powered by machine learning, or even some simpler data analysis, have the form of a more or less sophisticated dashboard. These kinds of application usually support only a tiny part of the whole business process and require a technician or a data analyst to trigger some maintenance actions manually.
We think that predictive algorithms are not solutions on their own, they are just tools which, properly used, should support a business process and make significant savings. And this does not only include a visualization of the current or predicted state, but it also supports the process of inspection, ordering parts, sending a crew, managing inventory and so on.
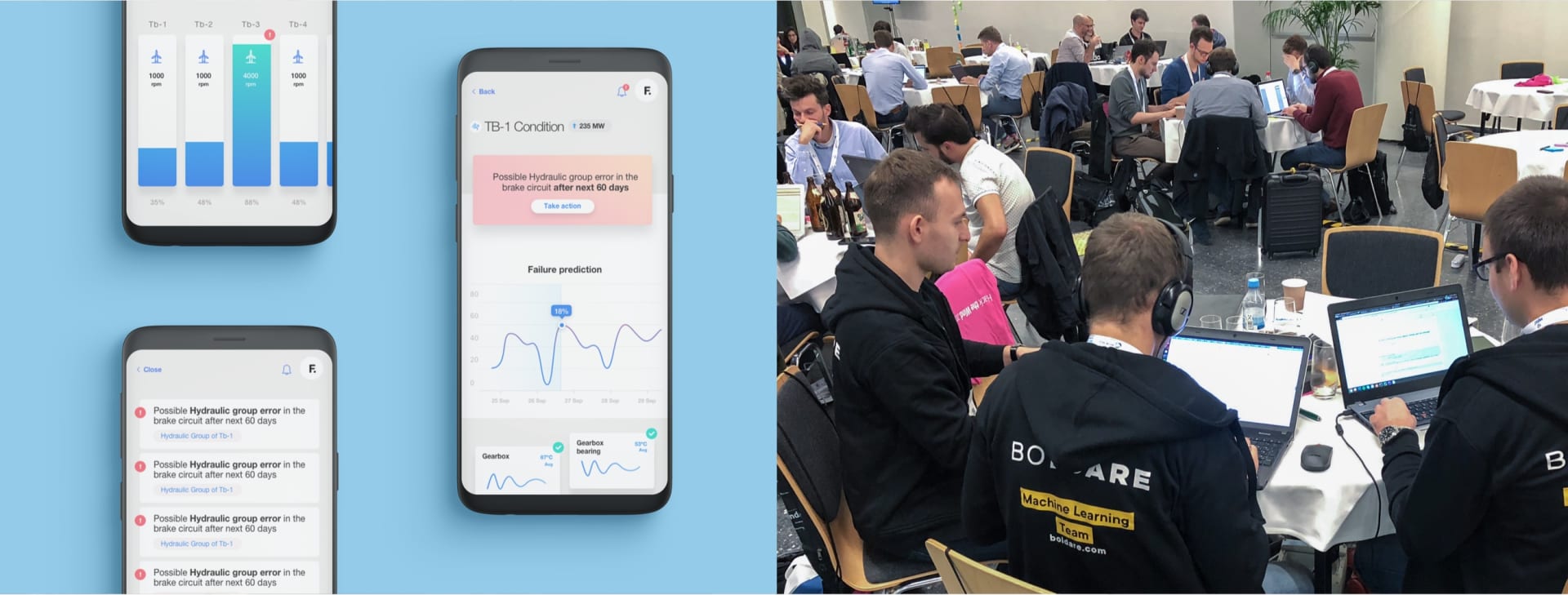
SCADA is the most common system for collecting wind turbine data. What are the advantages and disadvantages of that system?
Tomasz Bąk: We can name few advantages of SCADA like:
- The data from the SCADA system is relatively easily accessible.
- SCADA has the cheapest sensors.
- Data is collected as time-series, so it is quite easy to visualize and analyze.
However, SCADA isn’t perfect. You can find better data sources which give you a better failure lead time which is one of the main disadvantages of the SCADA system.
OK, so what other wind turbine data could be collected? And is it really worth it?
Tomasz Bąk: For instance, you can collect oil and grease data. This type of data can be analyzed automatically, and it is easy to make a visual inspection of it. By using this data for predictive maintenance, we can deliver better failure lead times, especially for bearings and gearboxes. However, the problem with oil and grease measurement is that the sensors are expensive.
Additionally, we could analyze vibrations. Vibration data gives the best failure lead time for bearings and gearboxes. In this case, we can distinguish two type of sensors: high and low frequency, but their cost is similar to the cost of oil and grease sensors.
Could you describe how your predictive algorithm works?
Paweł Krynicki: The family of the algorithms we use for this particular problem is called “supervised learning.” Internally they differ from each other a lot but in general, their way of working is the same: they take historical data and try to find a pattern which allows predicting a given value on a new dataset.
It’s called “supervised” because we supervise the process of learning: we know arbitrarily which observations are erroneous so the algorithm can calculate the overall cost of returning a specific set of values and then try to minimize that cost. Usually, the more data we obtain from the past, the better results we can get from the models. Then there are various techniques to clean up and process the data, normalize it or augment it with additional information.
In our case, we were given with a SCADA dataset containing measurements from various sensors of a wind turbine. Additionally, we obtained data from weather stations which allowed us to improve the results. Then we cleaned up and preprocessed the data by adding an additional dimension, aggregating and removing the outliers.
We also tested different approaches because as in the real world - we use what works best. We checked a recurrent neural network with Weibull distribution, various tree-like models and ended up with models trained for each component type, where some of them were simple decision trees and others, for instance, were using an ensemble technique called “boosting” in which we used several weak models which in fact didn’t perform well singly, connected them in a sequence and as a result we got a model which was much better.
To find the best moment to send the maintenance crew, we have optimized the hyperparameters of the model using a custom cost function - the estimated cost of shipping the inspection in a given point of time.
Is there only one solution or algorithm for predicting failures?
Paweł Krynicki: The number of ideas on how to predict failures with the best accuracy is endless. During the Hack The Wind hackathon our competitors used a Convolutional Neural Network which is usually used for datasets containing images. And this creative approach allowed them to outperform our model.
In the future, we will undoubtedly verify if this solution can be somehow connected with ours to get even better results. Also, there are various techniques and models for the time series data which can be adapted depending on the exact problem we are solving. Not to mention improving the results by obtaining new essential features which have an impact on the target variable.
How can you improve your algorithm?
Paweł Krynicki: We’re more than sure the results can be improved drastically. Don’t forget the results I was talking about were coming from a model trained on a dataset of only 5 wind turbines for only 1 year. We believe that when we gather more data, the performance can be improved, especially regarding prediction times (how much in advance it is returned before an actual failure occurs) and reducing the number of false positives - most probably this was also caused by the underfitting.
Also, we’ll be testing different methods and approaches, perhaps there is some model which would outperform the one we have created. Another way of improving the results is to find some new important features. Here the first thing which comes to my mind is the data from vibration sensors - this seems to be very effective for training ML models and gives very good results, but on the other hand, the sensors are quite expensive and not all wind farms are equipped with them.
The technical aspect of the machine learning solution is critical but invisible for the user. How do you make the ML algorithm results actionable for the user?
Paweł Capaja: Oh that’s easy. You provide them with an application which is the easiest to read and maximizes the potential of a reaction to the alerts it provides. We have prepared an app which not only shows the health of turbines’ components and prediction of possible failure but also helps the user to take action when the error occurs.
The app allows the creation of tasks and allows the user to schedule an inspection. By using geolocalization, it shows the technician the fastest way to the broken component and a smartphone camera can be used to scan the number of the component to speed up the replacement part ordering process.
What are your plans for further development of your predictive maintenance software?
Paweł Capaja: As a team, we decided that we want to continue the work started at Hack the Wind and develop the original idea further. We’ve decided to approach this in a startup manner. Currently, we have established the first business goals of the product, and we are validating our hypothesis; we are also contacting potential partners to interest them in our idea. Based on that, we want to develop our machine learning solution into a product. We are following the lean startup approach in our work to maximize the positive results.
What are the possible ways to collaborate with the Boldare Machine Learning Team?
Tomasz Bąk: We are still in the phase of product development, so we are looking for collaboration in different areas.
We would be happy to feed the predictive maintenance model with more data. It will help us to improve the quality of predictions.
It would be great to find some people with domain knowledge to cooperate. We have a few hypotheses about market expectations, which we want to verify with people from the industry.
Moreover, with such help, it will be possible to use that domain knowledge to increase the quality of predictions (we have experience in ML, but our contact with the wind energy sector is relatively recent). We have more experience in image recognition, ML models for customer activity (CHURN, marketing spendings optimization) or recommendation systems.
Thank you guys for this inspiring talk!
Three key takeaways from the interview:
- The cost and time of maintenance can be reduced significantly with predictive maintenance, but what’s more, a machine learning-based solution can elongate the lifespan of turbines and optimize energy production - in just 48 hours of coding we’ve managed to save 12.5K euros per turbine.
- Although data is limited, there is the possibility to improve the models by adjusting them and searching for new data sources, such as vibrations sensors.
- Predictive algorithms are just tools which should support other business processes, for example in the form of an app that can help plan and carry out the process of inspection, ordering parts, sending a crew, managing inventory and so on.
Learn more about Boldare’s solution for predictive maintenance and the team behind it.
The Boldare Machine Learning Team is an interdisciplinary team mixing various skills and levels of expertise. It contains, among others, machine learning engineers, JavaScript developers, and product designers. All team members have years of experience in commercial projects in their field of expertise. For the last year and a half they have been working together as a machine learning team, and as a team, they took part in the Hack the Wind competition. Their machine learning solution for predictive maintenance has been listed among the top 3 in the contest.
>> You can learn more about the Hack the Wind contest and the team who took part in it HERE
The product they have developed during the contest gained positive feedback at the WindEurope trade show. The ML team decided to further develop the product as a Boldare internal startup. If you would like to learn more about our predictive maintenance product for wind turbines you can read more in this case study.
Share this article: